Vibration Collection and Analysis
Vibration Collection and Analysis
VIBRATION START-UP:
Proper set-up will eliminate confusion and errors in the vibration data collection and analysis process.
ATS’ standard start-up procedures include a review of machine safety and accessibility for data collection, machine database set-up, digital pictures and report template set-up, route determination, data collection intervals, and applicable machine research. This start-up does not include the first collection of vibration data or a vibration analysis report.
One individual from your facility will accompany an ATS reliability consultant to review the supplied equipment list.
Minimizing variances in vibration data collection is critical for accurate analysis.
ATS’ vibration data is collected from each machine at both the driving and driven components. A complete set of data from ATS consists of three measurement directions from each bearing location (two in radial and one in axial). Based on bearing type and machine design, multiple measurements are incorporated including, but not limited to, acceleration and velocity. Data is downloaded and reviewed to ensure its integrity and spot imminent failures.
VIBRATION DATA ANALYSIS:
Accurate vibration data analysis measures asset health and leads to improved reliability through early detection of machine faults. Trending of the vibration amplitudes allows for the development of a rate of progression, which facilitates the convenient scheduling of repairs prior to failure. Overall maintenance costs and energy consumption are reduced as a result. Vibration analysis will often eliminate reoccurring problems by detecting the conditions that lead to premature failure, such as misalignment or looseness.
Appropriate vibration measurement specifications are paramount in the ATS data analysis process, which are based on expertise in data acquisition and machine design. ATS vibration analysis utilizes all data collection points without the assistance of alarm levels. The final assessment is based on multiple measurements per direction and at each collected location. The final recommendation will be based not only on the vibration signature, but also on the rate of change observed in relation to historical trending.
Each machine is allotted a full-page report consisting of supporting plots, a digital image, abbreviated explanation of the analysis, severity assessment, and recommended corrective action. Along with the reporting, a monthly summary is available which ranks each piece of equipment based on the assessed severity of identified problems.
Contact ATS today for information about vibration analysis.
Our Services
Service Offering Brochure
Vibration Collection and Analysis
Wireless and Wired Online Solutions and Management
Digital Dashboard
Program Consulting
Infrared Thermography
Steam Trap Survey
Oil Program
Motor and Circuit Analysis
Ultrasonic Leak Detection
Motion Amplification
Balancing
CNC Ballbar Analysis
Get in Touch
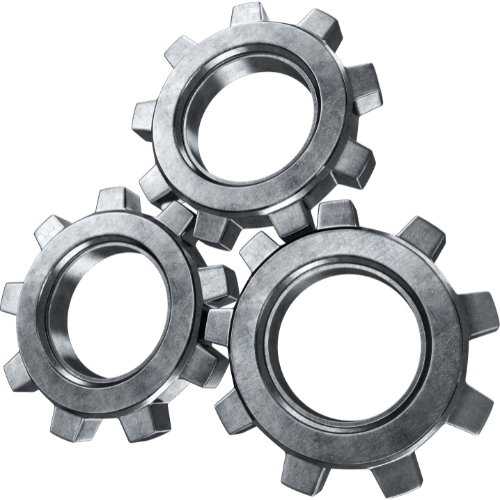