Ultrasonic Leak Detection
Ultrasonic Leak Detection
Utilizing ultrasonic leak detection within a predictive maintenance program will keep your system running more efficiently. Whether part of an energy conservation program or as fugitive emissions, leaks cost money, affect product quality, and can wreak havoc with the environment. Ultrasonic leak detection can often locate the problem, whether the leakage occurs in a liquid or gas system.
ULTRASONIC DETECTION ON ELECTRICAL EQUIPMENT:
Utilizing Ultrasonic Detection on electrical equipment can prevent catastrophic failure by detecting phenomena such as arcing, tracking, partial discharge and destructive corona. It is particularly effective on equipment not accessible to infrared scanning, such as high voltage enclosures (that do not have IR windows installed). Unlike Ultrasonic Leak Detection, cost quantification is not the main objective. Due to the nature of high voltage electrical equipment, any issues found using Ultrasonic Detection need to be addressed. This method can also be used on lower voltage enclosures where access is limited.
ATS will provide the labor and technology required to survey your facility and identify each leak. Surveyed systems within the facility will be documented by location and by unit designation. Data files of fault recordings will be documented as well. Images of the unit and fault location may be taken if needed.
Contact ATS today for information about ultrasonic leak detection.
Our Services
Service Offering Brochure
Vibration Collection and Analysis
Wireless and Wired Online Solutions and Management
Digital Dashboard
Program Consulting
Infrared Thermography
Steam Trap Survey
Oil Program
Motor and Circuit Analysis
Ultrasonic Leak Detection
Motion Amplification
Balancing
CNC Ballbar Analysis
Get in Touch
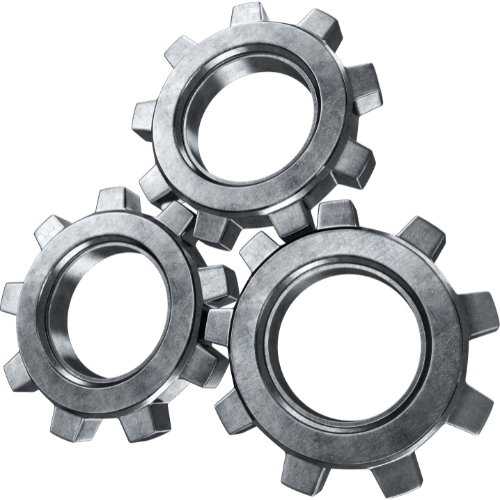