What Is PDM
What is PDM?
Predictive Maintenance (PdM), also known as condition-based maintenance, evaluates the condition of equipment by performing periodic or continuous (online) equipment condition monitoring.
The ultimate goal of PdM is to perform maintenance at a scheduled point in time when the maintenance activity is most cost-effective and before the equipment loses optimum performance. This is in contrast to a time-based program, where a piece of equipment gets maintained whether it needs it or not. Time-based maintenance is labor intensive, ineffective in identifying problems that develop between scheduled inspections, and is not cost-effective.
Benefits of Outsourcing PDM
No up-front capital required
Pay as you go with monthly purchase orders
You don’t have to worry about upgrades and software changes to PdM equipment – we take care of everything
Recognized leaders in Predictive Maintenance bring 256 combined years of service to your worksite
No vacations, no lay-offs, no transfers, bumping to other jobs, or light-duty restrictions
You get all of the service – none of the hassle
Remember When?
Remember when diagnosing a machine’s condition required nothing more than a screwdriver and a good ear? Well, technology has come a long way.
These days, a host of high-tech tools make it possible to accurately determine the condition of equipment as it operates. This information can then be used to make precise maintenance decisions. The results are improved productivity, lowered maintenance costs, and extended machinery life.
By pinpointing problem areas and hot spots long before they cause critical shutdown, Predictive Maintenance (PdM) also increases productivity:
TESTIMONIAL: In the beginning, we had little to no predictive technologies in place. It was a regular occurrence to not make it through a week without sending a production line home due to critical equipment being down. ATS assisted in establishing a vibration analysis program with data collected internally and analyzed by ATS. ATS then introduced us to IR technologies and started collecting and analyzing photos of our critical systems. With these programs in place we were able to convince our leadership to invest in a fulltime program of vibration, infrared, and oil analysis. … Implementing predictive technologies at our plant has been a key factor … in getting us to better than 97% uptime on all critical pieces of equipment. It is now a rare occurrence that a production line is sent home. – Brad, Household Appliances
Cost savings is one of the major motivations behind most Predictive Maintenance (PdM) Programs:
- One manufacturer of heavy machinery reduced its repair expenses by $1.7 million with Predictive Maintenance.
- Current estimates suggest that the average plant not currently using vibration analysis to monitor equipment can reduce its maintenance budget by 20% with PdM. This can save your company thousands-or even hundreds of thousands-of dollars each year.
- A major supplier to the U.S. government’s Defense and Aerospace Program avoided more than $1 million in downtime by doing an infrared thermography scan of its electrical distribution system.
Get in Touch
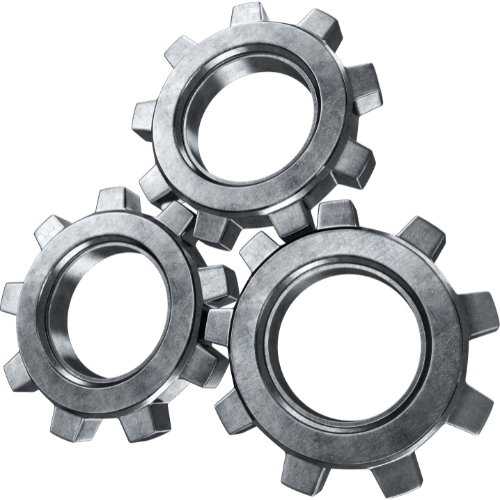